WHICH IS BETTER FOR HAND TOOLS?
Chromium-molybdenum (also called chrome molybdenum, chrome moly, or Cr-Mo) and chromium-vanadium (also called chrome vanadium or Cr-V) are names for two families of steel alloys used in hand tool manufacturing. Which one is better? When properly manufactured and heat treated, they are chemically almost identical and perform similarly.
WHICH IS BETTER FOR HAND TOOLS? Chromium-Molybdenum or Chromium-Vanadium Steel?
Chromium-molybdenum (also called chrome molybdenum, chrome moly, or Cr-Mo) and chromium-vanadium (also called chrome vanadium or Cr-V) are names for two families of steel alloys used in hand tool manufacturing. Which one is better? When properly manufactured and heat treated, they are chemically almost identical and perform similarly.
WHAT IS STEEL?
Steel is, by weight, mostly iron (often 90% or more) with small amounts of carbon (usually 0.1% to 2%) and sometimes alloying elements mixed in. Without heat treating and without alloying elements, steel is too soft for use in the best hand tools. By mixing in alloying elements and subjecting the mixture to high heat to change its hardness, we can modify mechanical properties like hardness, strength, toughness, and ductility.
Even in the best circumstances, however, some of these properties involve tradeoffs. For example, extremely hard steel will be strong, but also brittle. Instead of deforming elastically and then bouncing back when the stress is removed, hard steel will tend to break under high stress.
Some common steel properties include the following:
Hardness: a material’s resistance to wear and scratching.
Strength: a material’s ability to be stressed without becoming permanently deformed.
Ductility: a material's ability to become permanently deformed under stress before it breaks.
a material’s combination of strength and ductility that allows it to absorb energy without breaking.
HEAT TREATING
Heat treating means raising the temperature of steel and cooling it in precise, controlled steps to change its internal structure. At a microscopic level, steel is made of small grains, which are groups of metal atoms arranged in crystals.
Heat treating can alter both the grain sizes and the geometric arrangement of the atoms in the steel. Different grain sizes and arrangements react differently to stress. For example, larger grains slip past each other more easily, and this makes the steel softer than it would be with more small grains to resist movement better.
Heat treating can also change the arrangement of the atoms. Scientists have given names to different geometric arrangements, such as “austenite,” “ferrite,” and “martensite.” The same steel alloy has different properties depending on how the atoms are arranged.
ALLOYING ELEMENTS
Steel made of just iron and carbon is called “carbon steel.” It is not considered an alloy steel. Low-carbon steel, which has very little carbon, is weak and doesn’t respond well to heat treating. High-carbon steel also starts out weak but can be converted to a strong, brittle steel through heat treating.
Alloying elements can be added to iron and carbon to produce steel with desirable combinations of mechanical properties for specific applications. Common alloying elements include boron, chromium, manganese, molybdenum, nickel, and vanadium.
Here are some properties affected by these elements:
Boron: makes steel easier to harden.
Chromium: makes steel stronger, harder, and easier to harden; increases corrosion resistance. In high concentrations, it produces “stainless steel,” which highly resists corrosion.
Manganese: improves steel processing by limiting oxidation.
Molybdenum: makes steel stronger, harder, and easier to harden. Increases toughness at high strength.
Nickel: increases toughness at high strength. It also increases corrosion resistance.
Vanadium: increases toughness at high strength; reduces grain sizes.
WHAT STEEL SHOULD HAND TOOLS BE MADE OUT OF?
Although high-carbon steel may be appropriate for hand tools whose main requirement is a hard surface like some blades, most hand tools benefit from a combination of hardness, toughness, and corrosion resistance. Alloys like chromium-molybdenum and chromium-vanadium are more effective than high-carbon steel in achieving these combined properties.
Chromium-molybdenum specifically means a family of steel alloys that, when used for hand tools, have a moderate amount of carbon (often around 0.4% to 0.5%), around 1% chromium, around 0.15% to 0.20% molybdenum, and a range of other alloying elements. The name given by the Society of Automotive Engineers (SAE) usually follows the pattern 4XXX. For example, 4140 is a common chromium-molybdenum steel with 0.40% carbon, which is what the 40 in 4140 indicates.
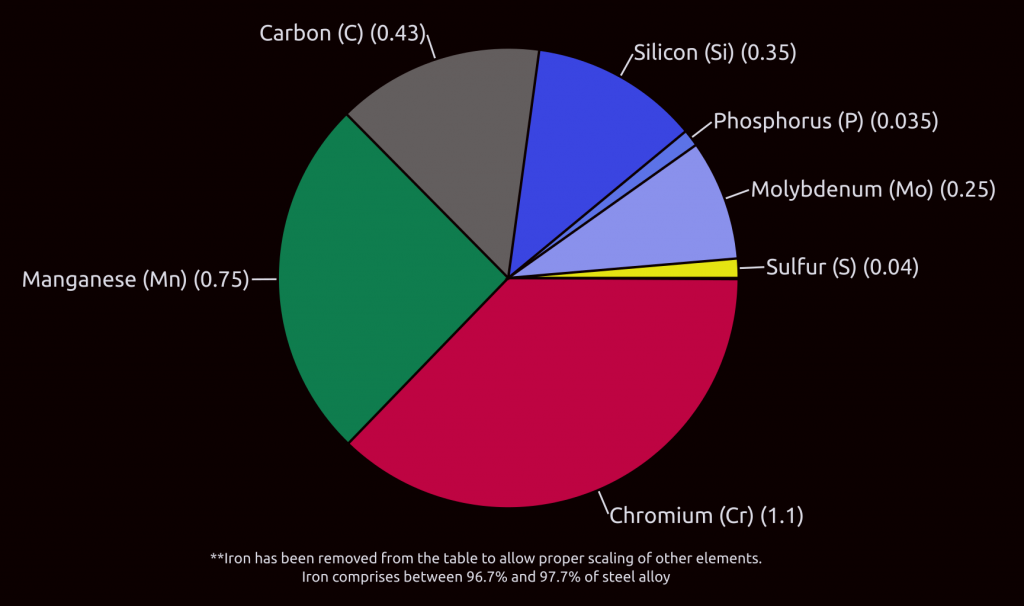
Chromium-vanadium specifically means a family of steel alloys that, when used for hand tools, have a moderate amount of carbon (often around 0.4% to 0.5%), around 1% chromium, around 0.15% - 0.20% vanadium, and a range of other alloying elements. The SAE name usually follows the pattern 6XXX. For example, 6150 is a common chromium-vanadium steel with 0.50% carbon, which is what the 50 in 6150 indicates.
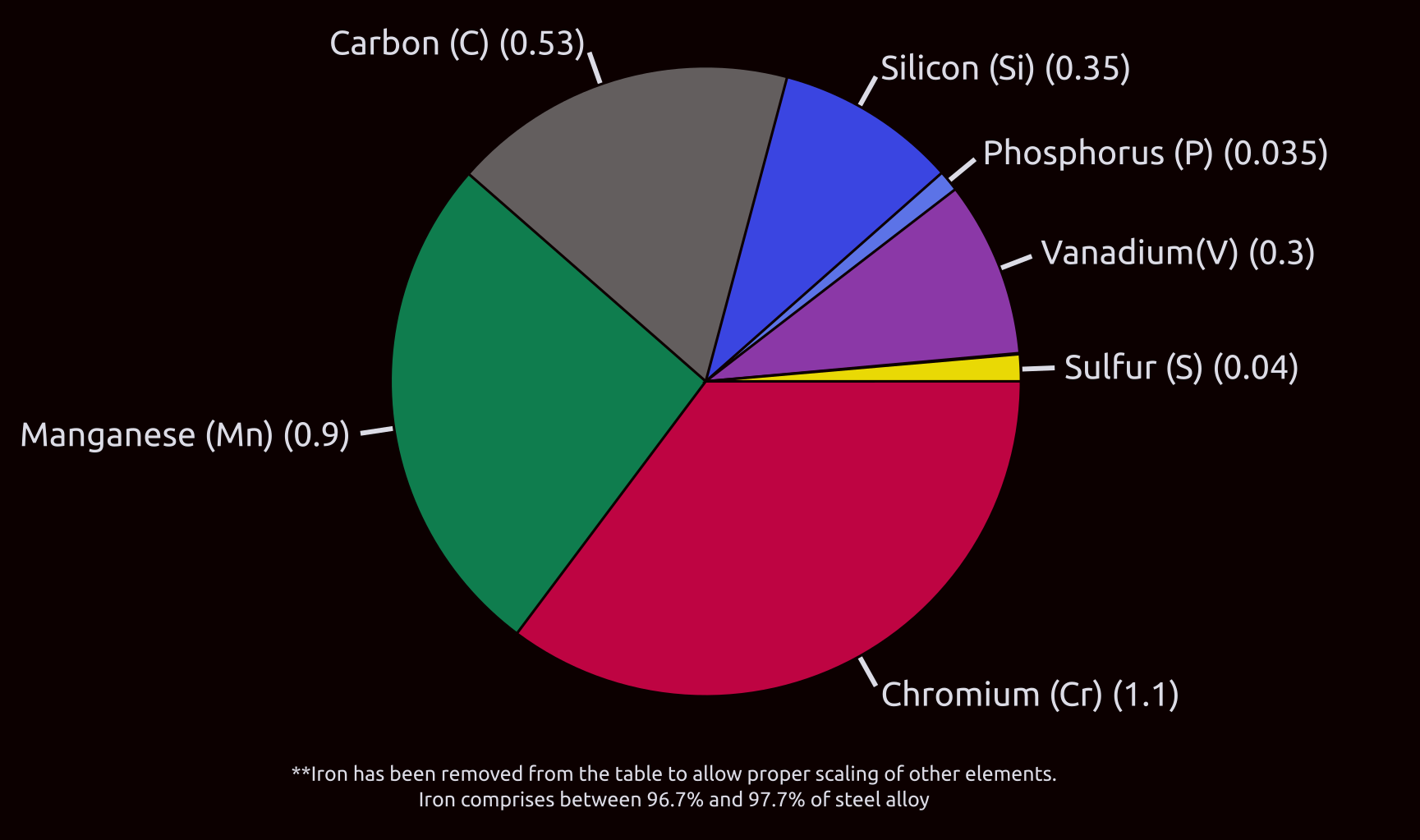
Chromium-molybdenum and chromium-vanadium produced with equal care and hardened to similar levels have highly similar mechanical properties. In fact, they are almost chemically identical, the main difference being far less than 0.5% by weight in the form of molybdenum or vanadium. Therefore, we cannot say that either chromium-molybdenum or chromium-vanadium is better. Either Cr-Mo or Cr-V is an excellent choice for all normal uses of wrenches, hand-driven sockets, impact sockets, ratchets, and other similar tools. The metallurgical difference between Cr-Mo and Cr-V is insignificant in these applications. Instead, the consistency of the material, the tool geometry, the hardness to which it is heated, and the design and implementation of the manufacturing process control the differences in hand tool quality.
Sometimes Cr-Mo tools cost more than Cr-V tools and tool users want to know the reason. The difference in cost is not typically because one steel is better than the other. Because of the similar intrinsic performance capabilities of Cr-Mo and Cr-V, the higher cost of Cr-Mo tools appears to be a marketing practice that’s hard to justify through science. Perceptions become self-fulfilling as tool users sometimes expect to see certain alloys on certain tools. Supply chains build up around these perceptions and that can make one steel alloy far more cost-effective than another for a particular product.
WHAT DOES CHISEN USE?
At CHISEN, we use, among other things, alloys from both the chromium-molybdenum and chromium-vanadium families to make our tools. Once supply chains are established across an industry, it can be most efficient not to vary steel types within those supply chains. For example, in our US supply chains, 4140 chromium-molybdenum is most readily available in the rolled sheet form we require to make our angle head wrenches and 8650 nickel chromium-molybdenum is most readily available for making our screwdrivers. For similar reasons, some of our hand-drive and impact sockets made in Taiwan use a 4140 Cr-Mo alloy and others use a 50BV30 Cr-V alloy. In all these cases, the alloys meet all performance specifications, and the choice comes down to supply chain dynamics and cost.
The manufacturing method can also affect our material selection. For example, the variation on chromium-vanadium called 50BV30 contains boron and works better for some tools forged in a cold state. The addition of boron allows the steel to be soft for cold forging and then, after forging, highly hardenable through heat treating.
If you have questions about CHISEN Tools' materials, please contact us.
- Combination Pliers
- Long Nose Pliers
- Diagonal Cutting Pliers
- Bent Nose Pliers
- Round Nose Pliers
- End Cutting Pliers
- Wire Stripper
- Mini Pliers
- Circlip Pliers
- Slip Joint Pliers
- Groove Joint Pliers
- Tower Pincers
- Locking Grip Pliers
- Fishing Pliers
- Wood Chisel
- Adjustable Wrench
- Combination Spanner
- Double Open End Spanner
- Double Offset Ring Spanner
- Hammer
- Axe
- Screwdriver
- Bit
- Bolt Cutter
- Pipe Wrench
- Aviation Snip
- Tin Snip
- Pruning Shear
- Pipe Cutter
- Cable Cutter
- Glass Cutter
- Hair Scissors
- Pet Scissors
- Kitchen Scissors
- Utility Knife
- Electrician Knife
- Saw
- New Universal Socket Wrench
- F Clamp for Wood Working
- Wood Turning Lathe